合成氨原料氣雙甲凈化精制工藝(簡稱雙甲工藝或醇烷化工藝)為我國自主知識產權的發(fā)明技術,是湖南安淳高新技術有限公司有關技術人員經過近20年不懈努力創(chuàng)造的技術。從1992年第1套工業(yè)化裝置在湖南衡陽氮肥廠投運至今,安淳人多次在技術的工業(yè)化適用性、工藝配套的節(jié)能性、工程設計的可行性及工藝優(yōu)化等方面進行了大量的工作,經過幾次大的技術提升及完善性的技術改造,創(chuàng)造了多種適應于不同生產類型、不同生產企業(yè)和不同生產條件的工業(yè)配套模式,極大地豐富了該技術的可適用性,節(jié)約了技術受讓企業(yè)的工程投資,創(chuàng)造了更大的經濟效益、社會效益及環(huán)保效益。到目前為止,雙甲工藝及其提升技術——醇烴化工藝已在全國中、小合成氨企業(yè)推廣40余家,投用的各企業(yè)均有其工程設計及技術實施方法的獨特性,特撰文加以總結。
1 雙甲(或醇烴化)工藝的基本原理
1.1基本反應原理
雙甲工藝首先以甲醇化反應來脫除脫碳后工藝氣中的CO和CO2(體積分數0.03%~0.30%),再以甲烷化反應將此氣體中的(CO+CO2)體積分數降至<15×10-6,完成對合成氨原料氣的凈化精制。
甲醇化反應反應主要以 CO,CO2與H2合成反應生成甲醇產品,并去除了原料氣中一定量的CO和CO2,這是雙甲工藝的第1步凈化反應的功能。受單程轉化率的限制,當反應器進口的未反應氣中的CO和CO2含量達到一定量時,要開循環(huán)機來提高醇的產率或降低反應氣出口氣中的(CO+CO2)的含量。
(2)甲烷化反應
甲烷化反應反應同樣以CO,CO2和H2為原料,生成CH4,主要目的是精制合成氨原料氣。為了減少循環(huán)氣的放空量,盡量要求進入甲烷化中的(CO+CO2)少,這也是雙甲工藝中比較注重的工程技術問題。
1.1.1 甲基化反應工藝
如果按市場要求生產甲醇外的其它產品,則可以在同樣的工藝條件下,在甲醇化反應器中裝填生產二甲醚類產品的催化劑,稱之為甲基化。甲基化主要反應方程式有:
CO+2H2=CH3OH
2CH3OH=CH3OCH3+H2O
H2O+CO=CO2+H2
總反應式為:3CO+3H2=CH3OCH3+CO2
1.1.2 醇烴化反應工藝
醇烴化反應是為了降低原料氣中H2的耗量。因甲烷化反應的生成物全部為CH4,必須在合成工段放空,增加了合成工段的氣耗和電耗。安淳公司開發(fā)了一種催化劑取代甲烷化催化劑對工藝氣體進行精制,此工藝稱為醇烴化精制工藝。反應是在單催化劑床層的精制反應器內完成,氣體中大部分的(CO+CO2)與H2進行醇化反應,少量進行烴化反應,生成多元醇類、極少量烴類和水的混合物,并以液態(tài)副產品輸出,使合成工段循環(huán)氣放空量基本不增加。輸出的副產品可進入甲醇精餾工段回收多元醇類產品,再與甲醇精餾后的殘液一起作燃料使用。當然,也可直接將醇烴化液作燃料使用。醇烴化反應主要方程式為:
CO+2H2=CH3OH(醇化反應)
CO2+3H2=CH3OH+H2O(醇化反應)
(2n+1)H2+nCO→CnH(2n+2)+nH2O
2nH2+nCO→CnH2n+nH2O
2nH2+nCO→CnH(2n+2)O+(n-1)H2O
(3n+1)H2+nCO2→CnH(2n+2)+2nH2O
從上述各種反應可知,原料氣不但可以按新的凈化精制方式進行處理,而且還可以通過加入不同的催化劑來調節(jié)產品品種和副產物生成量,同時也調節(jié)了原料氣中有效氣體的消耗量。
由于碳原子在分子中以多碳結構存在,也就是說碳原子形成了“鏈”,這樣的分子結構形態(tài)就可以減少H2的耗量。
通過優(yōu)化改進醇烴化催化劑的配方,目前通過醇烴化精制生產出的副產物主要成分質量分數為:水39%、甲醇33%、乙醇15%、其它多元醇13%。
由于是液態(tài)取樣,生成的甲烷及其它常溫下揮發(fā)的二甲醚類等物質未檢出。由于醇烴化產品大部分為醇類物質,完全可以作為清潔燃料使用。
1.2 雙甲工藝在合成氨工藝中的設置及流程
1.2.1 雙甲工藝的基本原則流程
來自造氣工段的半水煤氣經氣柜后進行粗脫硫(使H2S質量濃度<0.07 g/m3,標態(tài)=,然后加壓進入中變;出中變的氣體中CO體積分數控制在1.5%~5.0%(具體量視產醇量的多少,即按特定的氨醇比,依物料需要量決定),經脫碳后使CO2體積分數降至0.2%~0.5%,再用無硫氨水進行二次脫硫,將H2S體積分數脫除至100×10-6以下;再進行精脫硫,使氣體中的總硫體積分數降至0.1×10-6;氣體入高壓機壓縮(壓力的配置與甲醇產量有關,原則上甲醇產量高時取較低的生產壓力;以凈化為目的時,為了得到較高的轉化率和較好的熱利用率,壓力可取得高些),然后與反應后的高溫醇后氣進行換熱,溫度為200℃時進入甲醇化塔;出甲醇化塔的氣體與新鮮氣換熱,再水冷至40℃左右進入醇分,經醇分后的氣體中(CO+CO2)體積分數達到0.03%~0.30%。這里有多種方式進入下一步精制崗位:①以這個壓力等級直接進行醇烴化或甲烷化反應,再經高壓機加壓后送入氨合成工段;②將氣體送入高壓機加壓至與氨合成相等壓力后再進入甲烷化系統(或醇烴化系統)反應?傮w來說可達到反應后的原料氣中(CO+CO2)體積分數≤10×10-6,氣體再經換熱、冷卻、分離水分后送往氨合成系統。從氨合成系統中排出的吹除氣及液氨貯罐排出的弛放氣經脫氨后去氫回收裝置(真空纖維膜或變壓吸附),回收的H2返回合成氨系統,剩余的氣體則排空。如果采用醇烴化精制工藝,在醇烴化工序的水分離器中分離出的醇類和烴類混合物可直接進入甲醇精餾工序或直接作為燃料使用。
1.2.2 醇產量要求高時(醇氨比大)的原則流程
雙甲工藝的目的是以凈化精制原料氣為主,副產甲醇為輔。但隨著市場變化,產品需求量也在變化,產品結構必須隨時調整。即要求醇氨比可進行大幅度調節(jié),在甲醇市場銷售情況好時,醇氨比要求達到1∶3或更高的指標,此時產醇和精制原料氣成為雙甲工藝的雙重任務。
在這種條件下,流程安排原則上是設置2臺甲醇塔,第1甲醇塔的作用是產醇(盡量放在低壓級),第2甲醇塔的目的是凈化(可設置在高一點的壓力等級)。經過第2甲醇塔后,氣體中的(CO+CO2)體積分數≤0.3%(在該指標下新鮮氣消耗不多,又可提高熱利用率,且操作便捷)。第1級甲醇化的操作壓力可以采用3.0 MPa或 8.0MPa,第2級甲醇化及甲烷化、氨合成操作壓力采用12~32MPa,其原則流程見圖1。
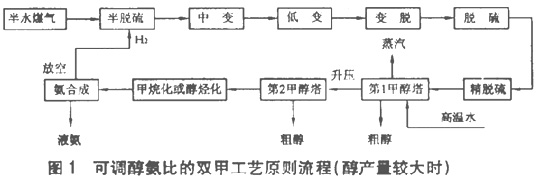
當聯產甲醇的任務較重、醇氨比很大時,原料氣全部通過2臺塔,其中第1甲醇塔設置部分氣體循環(huán),氣體中80%的CO與CO2轉化為甲醇,當然也可以甲基化生產二甲醚或其它產品;第2甲醇塔轉化剩余的CO和CO2,塔出口的(CO+CO2)體積分數≤0.3%。
如果甲醇市場需求疲軟,雙甲工藝則以凈化精制為主,甲醇為副產品,要求盡量減少產量。在實踐中,有的企業(yè)將醇氨比降至1∶10甚至1∶20,此情況下可只用1臺甲醇塔來完成凈化,運行中可不啟用循環(huán)機,第2甲醇塔作為備用塔,同樣能控制入甲烷化爐的(CO+CO2)體積分數≤0.3%。
此流程的優(yōu)點是:在低壓下合成甲醇,占整個原料氣6%~10%的氣體(CO,CO2和生成甲醇需要的H2)無需加壓至更高壓力,大大節(jié)省了電能;在3.0~8.0MPa下甲醇化,可利用甲醇化反應熱副產3.9MPa蒸汽(噸醇副產1.2~1.5t蒸汽),此蒸汽經過熱后可作為動力使用,背壓后的蒸汽仍可作為工藝用汽,且由于用飽和水來調節(jié)甲醇化塔的催化劑層溫度,此壓力下的水溫正是甲醇催化劑最佳活性操作溫度,使用效率最高,溫度調節(jié)也十分方便可靠;由于采用了甲烷化與氨合成等壓下反應,可免除工藝氣再次壓縮而被污染的缺陷,也可以較方便地利用氨合成反應熱,維持低成分下[(CO+CO2)體積分數≤0.3%]甲烷化反應溫度。
2 幾種典型的雙甲(或醇烴化)工藝的工程設計模式
2.1 不同壓力等級組合的設計模式
2.1.1 等壓雙甲凈化工藝設計模式
1992年第1套雙甲工藝在湖南衡陽氮肥廠投產,但因國內的常溫精脫硫技術尚未實現工業(yè)化,采用了在甲醇化塔催化劑的上部設置高溫氧化鋅精脫硫劑的方式進行精脫硫。由于當時甲醇銷售情況較好,安淳公司在工程設計中采用了雙塔可串聯可并聯運行的甲醇化工序設計方式,生產中將變換出口氣中的CO體積分數提高至5%以上,得到了甲醇產量較高、甲烷化精制效果也好的效果。后再經優(yōu)化設計,湖南郴州地區(qū)橋口氮肥廠、山西豐喜集團臨猗分公司、湖南湘陰氮肥廠、吉林梅河口化肥廠等企業(yè)都采用了這種在12.5~15.0MPa等壓力級條件下的雙甲工藝模式。
本流程比較適合于已有該壓力等級聯醇崗位的企業(yè)、由銅洗改造成雙甲工藝的企業(yè)(即在壓縮機五出或六出由原來進入銅洗工段的管道上接雙甲工藝),也適合于以凈化精制合成氨原料氣為主的企業(yè)。目前銅系甲醇催化劑已經能在此壓力下獲得很高的轉化率,可認為即使再提高壓力也不會使甲醇化的轉化率大幅提高。基于此,對于以凈化為目的而設雙甲工藝的企業(yè),首先推薦這種模式來完成工程設計,如山西晉豐集團高平化肥廠、山西晉豐集團聞喜化肥廠、江蘇華爾潤化工有限公司、山東德齊龍化工有限公司等企業(yè)均采用了這種配置方式。
這種配置工藝的最大優(yōu)點是:甲醇化后的氣體不要經過壓縮,減少了被壓縮油污染的氣體對甲烷化或醇烴化催化劑的影響;雙甲系統設在同一個壓力等級,便于兩工序循環(huán)機的共用,也便于操作管理;可以利用甲醇化的反應熱來加熱醇烴化或甲烷化的入爐氣體;可以利用原銅洗的高壓設備來改作甲烷化或醇烴化設備。
值得注意的是,由于甲醇和二甲醚等會影響甲烷化催化劑的反應活性,如采用甲烷化反應進行精制(醇烷化工藝),則必須要考慮在甲醇化后設置洗醇崗位,以軟水來洗凈尾氣中的微量甲醇和二甲醚,達到保護甲烷化催化劑之目的。
這種配置的典型流程見圖2。
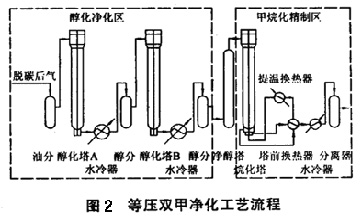
2.1.2 與氨合成系統等壓的雙甲凈化工藝設計模式
當有部分高壓設備可供利用,而雙甲工藝又是以凈化為目的時,也可考慮將雙甲工段與氨合成壓力等壓的流程進行系統設計。
這種方式特別適合于氨合成系統改造和凈化精制改造一起進行的工程。例如2001年邯鋼集團化肥廠進行φ1600mm氨合成系統改造,原氨合成系統有很多設備可供利用,為此設計了1套醇化和甲烷化均為32MPa的雙甲凈化精制系統。該裝置已運行近6年,目前運行狀況良好。以后又相繼有部分企業(yè)也采用本設計方式進行了系統配套。
這種設計方式的優(yōu)點是:可利用原氨合成的舊設備,以提高催化劑的利用率和甲醇化的生產能力;在高壓下運行,催化劑使用空速可適當提高,系統熱利用率也高,熱損失相對也較小,還可以提高反應速率;經過雙甲工藝后的氣體無需壓縮機增壓,減少了氣體被壓縮機油污染的機會,更大程度地保護了氨合成催化劑。其缺點是:當產醇量較高時,將會使制醇氣體壓縮功耗增加(經計算,生產1 t甲醇的原料氣由12.5 MPa壓縮至 26.0MPa,壓縮機將增加電耗53kW·h);提高醇化反應壓力并不能較大幅度地提高甲醇化的轉化率,也就是說,10MPa以上的甲醇化反應,利用目前銅系催化劑,轉化率提高相當有限,相反還會增加副反應,使甲醇產品質量受到影響。
本工藝的基本流程與圖3相同。
2.1.3 在12.5~32.0MPa下的等壓醇烴化凈化精制工藝
按上述2.1.1和2.1.2的配置方式設計的雙甲系統,同樣適用于醇烴化工藝。在2000年以后,為了提高雙甲工藝的技術水平、降低能耗、提高氣體利用率,又開發(fā)了醇烴化工藝。工藝先期是采用醇化后串烴化的方法,烴化反應主要采用烴化催化劑來實現。由于烴化反應選擇性強、要求溫度控制在一定的范圍,為了更有其工程可行性或實用性,后期又開發(fā)了更加方便的甲醇化再串醇烴化的工藝方式。也就是說,在原來裝甲烷化催化劑的反應爐內,換裝上醇烴化催化劑(同時完成醇化和部分烴化反應,故稱之為醇烴化),既達到了盡量多產醇類產品的目的,又使深度精制滿足合成氣的要求。
醇烴化技術是安淳公司自身技術不斷完善的產物,是雙甲工藝的提升技術。其基本原理是利用甲醇工序對合成氨原料氣進行醇化反應并副產甲醇產品,同時對氣體中的CO和CO2進行初步脫除,再利用醇烴化工序的醇烴化反應(原來為甲烷化工序)進行合成氨原料氣的進一步精制,并副產醇類和烴類混合物。工藝的第1步是將CO和CO2轉化成CH3OH,使(CO+CO2)體積分數下降至0.03%~0.30%;第2步是將少量的 CO和CO2在醇烴化反應器內轉化為低碳烴類物、低碳醇類物、甲醇和少量甲烷,最后使精制氣中的(CO+CO2)體積分數低于10×10-6再進入氨的合成崗位。這種工程設計可取消醇化后的凈醇處理工作,簡化了流程,降低了消耗。
安淳公司在山東德齊龍化工有限公司兩套“18·30”工程、天脊集團晉城化工公司等企業(yè)均采用了這樣的設計方式,其流程見圖3。
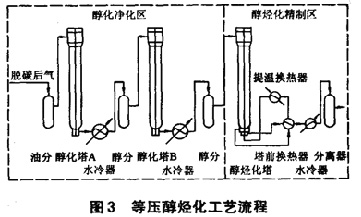
2.1.4 不等壓的雙甲(或醇烴化)工藝設計模式
(1)如前所述,醇化工序、甲烷化(或醇烴化)工序可以設置在同一個壓力級下,也可以按企業(yè)實際情況設置在不同壓力下操作。采用該設計模式,已為多家企業(yè)的醇烴化工藝進行了設計或改造,均收到了很好的效果。
(2)另一種方式是將一級和二級甲醇化反應放在同一個壓力級,將甲烷化(或醇烴化)設置在另一個壓力級。流程中只有一個區(qū)別,即采用甲烷化進行精制時,必須在甲醇化后設置醇洗工序。由于甲醇化后的氣體要再次進入壓縮工序,必須進行除油處理以保證醇烴化或甲烷化催化劑的安全。典型流程見圖4。
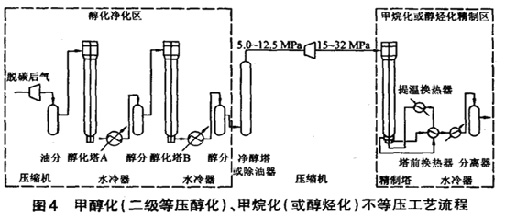
圖5所示流程的優(yōu)點是兩級甲醇化均在同一壓力等級下進行反應,這對已有聯醇及聯醇設備的企業(yè)改造成雙甲工藝時,工程量相對較小。
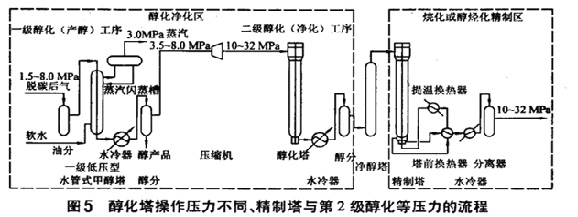
該流程可獲得較高的甲醇產量,二級甲醇化的(CO+CO2)的轉化率也可以達到很大[第2級甲醇化后的(CO+CO2)體積分數可以達到 0.03%)],且可共用循環(huán)機。2臺甲醇化塔可串可并,也可以一塔操作而另一塔更換催化劑和升溫還原。當甲醇產量較低時,可只投運1臺塔,另一臺塔作為備用,且調配十分方便。這樣就可保證將催化劑活性較好的塔設置在第2級,保證了對原料氣的深度凈化的要求。
甲烷化或醇烴化如果設在更高的壓力等級,則可使用舊的氨合成系統設備,這將減少甲烷化催化劑或醇烴化催化劑的用量,并可提高精制度,也有利于從合成崗位取熱用于甲烷化爐或醇烴化爐。該流程的缺點是流程相對較長,在甲醇化和甲烷化中要設置除油或凈醇工序,而且壓力等級的不同也會給生產管理及其操作帶來一定的不便。
(3)圖5是最近在山東德齊龍化工有限公司研制投用成功的一種全新的流程,其優(yōu)點是產醇量很大,噸醇可副產高品位蒸汽(3.9 MPa)1.2~1.5t,只要將產生的蒸汽在其它崗位進行過熱后,就可以進行差壓發(fā)電,發(fā)電后的背壓蒸汽還可作為工藝用汽。
由于第1級甲醇化在低壓下完成,可降低壓縮功耗,這非常符合安淳公司提出的產醇在低壓下進行、凈化精制在高壓下進行的工藝理念。
該流程的另一個優(yōu)點是第1級甲醇化塔產醇量無論多大,因是采用3.9 MPa的飽和水來調節(jié)催化劑床層的溫度,比傳統的氣氣換熱反應器調溫方便、操作安全性強。但這種流程不太適合于產醇量較小的企業(yè),其原因是第1級甲醇化塔投資較大,流程也較長。
當然,也可以將第1級甲醇化塔設為普通的氣氣換熱方式的反應器,雖然回收的蒸汽量較少、蒸汽品位較低(0.2 MPa左右),但卻比較適合于已有該壓力等級聯醇系統的企業(yè),操作也有相當成熟的經驗。但從反應機理來看,不主張大量生產甲醇的塔采用冷激式降溫,這對熱回收、降低循環(huán)量、保護甲醇催化劑和提高產品質量等方面均沒有好處。
2.1.5 不同壓力級配置的雙甲工程設計小結
10多年來,安淳公司為用戶設計了40多套凈化精制工藝,運用了各工序的多種壓力級配置的設計方式。這些設計方法是完全按照使用企業(yè)的具體情況而定,最主要是運用了雙甲工藝的專利技術核心內容——甲醇化后串甲烷化(或串醇烴化)凈化精制合成氨原料氣。至于各工序壓力級的配置,關鍵是要使反應器和催化劑發(fā)揮最大效益,要使系統能力達最大化、安全化,要使系統流程最為簡化,最終達到綜合效益最好。
2.2 雙甲工藝不同產出物的工程設計方式
雙甲工藝有2~3臺反應器,原料CO,CO2與 H2在每臺反應器內發(fā)生催化反應,控制不同的反應條件和相應的催化劑,在理論上可以得到多種有機化合物。
目前最為成熟的方式可以得到甲醇和二甲醚及甲烷或多元醇烴類物質,如果進一步研究也可以得到汽油的替代物。安淳公司在雙甲工藝中采用了不同的催化劑,也創(chuàng)造了幾種產品生成物的設計方式。
2.2.1 生產醇醚燃料
1996年在湖南湘陰氮肥廠的雙甲工藝改造中,在甲醇化爐內裝填安淳公司研制的醇醚催化劑,生產出的醇醚混合物作為民用醇醚燃料進行推廣,取得了可喜的成果,也為一步法合成二甲醚進行了前瞻性的工作,目前正在進行一步法生產二甲醚的深入研究工作。如果再采用相配套的精餾方式,可以同時得到甲醇和二甲醚兩種產品。這種工藝為甲醇生產企業(yè)生產二甲醚提供了經驗,也為利用本系統流程生產其它碳一化工產品提供了經驗。工藝流程見圖6。
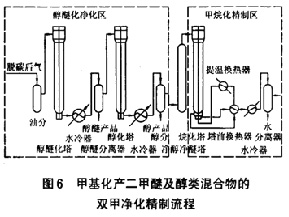
這種配置方式的優(yōu)點是為小型化肥企業(yè),特別是碳銨企業(yè),在肥料銷售淡季可向市場提供甲醇或醇醚產品,提高了企業(yè)的效益,也為雙甲工藝走向多元化產品之路提供了條件。
2.2.2 優(yōu)質燃料
與圖4流程一樣,如果將甲烷化內的催化劑換成醇烴化催化劑,或將其催化劑配方優(yōu)化,或生產出多元醇產品的優(yōu)質燃料,再通過精餾可得到甲醇產品。也就是說,甲烷化精制生成的副產物為氣態(tài)的甲烷,其只能隨氣體進入氨合成工段以放空的形式排放;而醇烴化精制生產的副產品絕大部分為液態(tài)的多元醇類產品,可用以代替液化氣作為燃料出售,因而具有更高的經濟和環(huán)保效益。
該產物也可作為燃料進入鍋爐或造氣系統,也可以送入甲醇精餾系統,經回收其中的甲醇后,其余物質隨甲醇精餾的殘液送入鍋爐或造氣系統。
如果對醇烴化催化劑再作進一步研究,使生成物向人造汽油方向轉化,將會有更大的使用效益和十分可觀的經濟利益,當然這種研究的成功將有待時日。
從環(huán)保的角度來說,甲烷化工藝生成的甲烷不能向大氣排放,醇烴化產生的物質也絕對不能外排,兩者均以燃料的形式進入系統燃燒,提供熱量供工藝系統用,這也是很簡便的處理方式。
這種工藝改進的方式直接帶來了原料氣中 H2消耗量比同樣條件下甲烷化反應下降近24%,也使合成放空量減少80%。
2.3 采用不同醇氨比設計的雙甲工藝
安淳公司在20世紀90年代初期已申請了可調醇氨比的雙甲工藝的技術發(fā)明專利技術,其核心內容是運用了雙級甲醇系統的工程設計方式,第1級甲醇系統著眼于多產甲醇,第2級甲醇系統立足于對原料氣進行深度凈化。這樣,整個工序運行可以十分安全地應付甲醇產量的變化或氣量的變化,在催化劑投用初期、中期和末期均能十分方便地調節(jié)系統,達到系統始終處于高效節(jié)能的運行狀態(tài)。
在工程實踐中,有的企業(yè)醇氨比達到了1∶2(湖南衡陽市氮肥廠、山東德齊龍化工有限公司)或更高,而以凈化為目的的企業(yè)只有1∶20(山東德齊龍化工有限公司、邯鋼集團化肥廠、河南心連心化工有限公司等),系統運行均十分安全可靠,進入烷化或醇烴化的氣體中的(CO+CO2)體積分數小于0.3%,最低的可達到0.03%。當然,甲烷化或醇烴化的外供熱也相應有所增加。
實踐證明,由于雙甲工藝集凈化、精制原料氣和生產甲醇、二甲醚等類甲基產品或雙甲燃料產品于一身,本身也是一個十分重要的、工藝中不可或缺的崗位,必須能長周期運行,催化劑的更換只能在有計劃性的檢修條件下進行。采用雙級甲醇化的工程理念是建立在要十分安全地運行雙甲工藝的基礎條件上,這也在近20年來的雙甲工藝運行實踐中得到了證實。
2.4 精制工序不同外供熱的設計方式
通過對醇化串醇烴化或甲烷化各反應器的熱量衡算及工程實踐證明,采用甲烷化反應方式作為精制時,要達到甲烷化爐內的反應熱量平衡,通常的控制指標是使進入甲烷化爐內的(CO+CO2)體積分數>0.7%,進入醇烴化爐的(CO+CO2)體積分數>0.5%(因醇烴化反應比甲烷化反應溫度低)。如果采用這樣的成分入甲烷化爐,將會有較多的CH4生成,也會增加原料氣中 H2的消耗量,造成合成工段放空量增加。如果進入醇烴化工段,也會使副產的多元醇類產品增加,造成精餾負荷增加。因此在工程上要盡量降低這個指標,使有效氣體盡量多生產甲醇類產品。
一般是將進入醇烴化或甲烷化的(CO+CO2)體積分數定為0.03%~0.30%,這樣勢必在精制工段要采用外供部分熱量來保證反應器正常運行。當然,如果生產的是人造汽油或民用燃料時,則要求產品產量愈高愈好,此時工藝將會有較大的調整。
以年產100kt氨副產31.3kt粗醇為例,變換氣中CO體積分數為4.31%,原料氣中CO體積分數為5.95%,CO2體積分數為0.31%,醇后氣中 CO及CO2體積分數與補充熱量(以電功率計算)的關系見表1。
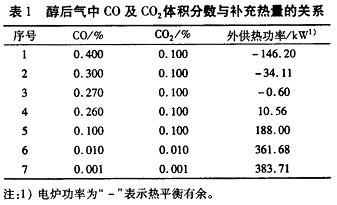
由表1看出,不計熱損失,也不考慮有水冷器部分的熱量損失的條件下,只考慮反應平衡,在(CO+CO2)體積分數為0.37%時(序號3)無需外供熱,但(CO+CO2)體積分數下降至0.36%時(序號4)需外供熱10.56kW;(CO+CO2)體積分數降至0.2%時,外供熱增加至188.00 kW,即(CO+CO2)體積分數下降了44%,外供熱增加 16.8倍;隨著(CO+CO2)體積分數的降低,外供熱隨之也增加,直至(CO+CO2)體積分數為 0.002%時,外供熱(電)達到383.71 kW。
一般來說,要維持低組分下的反應熱平衡,要盡量降低進入水冷器的氣體溫度,并提高催化劑活性(提高轉化率),更不能啟用循環(huán)機(否則會使系統的熱損失更大)。當然,實際工程中要考慮多種因素,因而要留有充分的余量來設計系統。在雙甲工藝的工程設計中,可采用多種方式向系統補熱。
(1)用發(fā)電蒸汽取熱的方式
該方式是采用蒸汽加熱器加熱甲烷化塔或醇烴化塔進口氣體,過熱蒸汽溫度在260℃以上,將醇烴化塔進口氣體的溫度由190~200℃加熱至 210~220℃(采用甲烷化精制時,溫度至少要再提高20℃以上)。河南心連心化工有限公司、湖南岳陽天潤化工有限公司等企業(yè)均采用這種方式來補充熱量,系統采用原合成系統的舊廢熱鍋爐來實現本工藝,加熱流程見圖7。
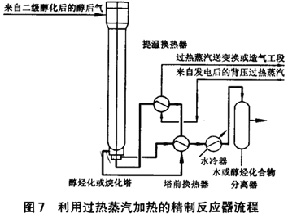
該流程的優(yōu)點是:間接加熱氣體,無需設置內外均是耐高溫和能承受高壓的氣氣換熱器;安全可靠;可以利用舊的合成塔廢鍋。該方式必須有過熱蒸汽的來源,換熱過程是取蒸汽的顯熱,沒有一定的蒸汽流量也不會使加熱過程順利。
(2)利用變換系統的熱量
當變換為中變串低變流程時,可利用中溫變換爐出口310~400℃的反應出口氣,利用傳熱介質來間接加熱甲烷化塔或醇烴化塔的進口氣體。該流程可在變換爐出口設1個U形管換熱器,管外走變換氣,管內走傳熱介質;同時在醇烴化塔或甲烷化塔的進口設1個U形管換熱器,管內走高壓入口氣,管外走傳熱介質,利用傳熱介質的流量來調節(jié)加熱入爐氣。
這種流程相對簡單,不是用氣氣直接換熱的高溫高壓換熱器來加熱,從而減少了因換熱器泄漏造成氨合成塔內催化劑中毒的可能性。但該流程必須與中溫變換相配套,如果采用全低變工藝,因反應氣溫度與甲醇化和甲烷化反應溫度相近,無法用此方法來換熱。
(3)利用合成工段的出口氣熱量
該加熱方式在1996年就已提出,也進行過詳細的流程考慮,其流程如圖8所示。這種取熱方式的優(yōu)點是可以長期利用合成系統的高溫反應熱,只要換熱器設計合理、系統開停車安全性及各管線和閥門用材料考慮周到,基本上是可以穩(wěn)定運行的。
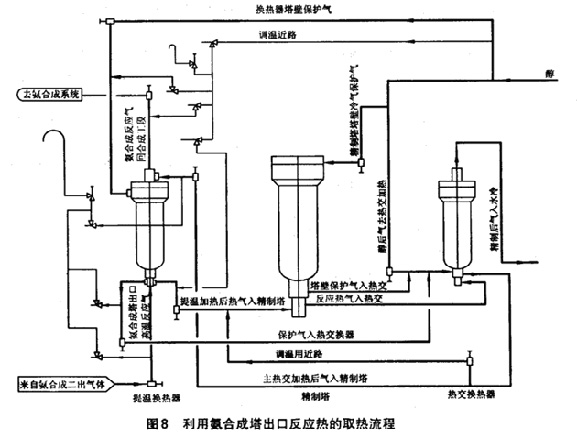
但該流程很復雜,需要增加1臺抗氫腐蝕且能耐高壓的設備于合成塔二出入廢熱鍋爐的管線中,采用氣氣直接換熱的方式,為了使內件壓差不至于太大而造成內件設計更為困難,最好是將合成與精制壓力設置在同一個壓力等級;由于需要使用抗氫蝕、耐高溫的特種管材,為了減少此特種材料的用量,要求氨合成系統與凈化精制系統位置相距不遠;該流程中有多個相關聯的換熱器,具體是合成系統的塔外換熱器、精制部分的塔外換熱器及跨工序的提溫換熱器,假若提溫換熱器在苛刻的條件下運行一旦發(fā)生泄漏,造成未精制的(CO+CO2)體積分數在0.03%~0.30%的原料氣進入氨合成工段,會導致氨合成催化劑中毒,且氨合成系統熱交換器的熱負荷和醇化部分塔外換熱器的熱負荷也會相應變化。基于上述原因,限制了其使用范圍,安淳公司更多的是考慮用其它方式來取熱用于精制塔。
同樣是在合成塔部分取熱,安淳公司也研發(fā)了一種間接換熱方式,即將耐熱介質加熱后,再通過另外的間接加熱器將熱量傳遞給精制塔進口氣體。這種取熱方式已在河南晉開醇烴化工程、貴州開磷集團劍江化肥有限公司的醇烴化工程中被采用。
(4)從造氣工段、鍋爐工段取高溫熱
在合成氨企業(yè),只要有溫度穩(wěn)定在300℃以上的熱源就可以用來加熱精制塔進口氣體。在造氣工段的吹風氣回收鍋爐內或在鍋爐工段的省煤器前設1臺加熱器,用間接換熱的辦法,同樣利用傳熱介質來加熱精制塔入口氣。但設備設計可靠性研究及工段取熱的方便性將要視為工程設計的重點,取熱方式將視企業(yè)的具體情況因地制宜選擇。
(5)適當控制精制塔入口氣體成分,采用電爐直接加熱
通過表1可知,當氣體中的(CO+CO2)含量達到一定值時,可使外供熱量減少或無需外供熱。但為了降低H2的消耗,盡量要使進入精制塔內氣體中的(CO+CO2)量低一些,這就存在一個優(yōu)化操作控制的問題。
安淳公司不主張將這個指標降得過低,一般進入精制塔的(CO+CO2)體積分數約0.3%就可以了,這樣所需外加熱量不多,操作也方便。
由表2可以發(fā)現,在(CO+CO2)體積分數為 0.3%左右時,氣體消耗量增加并不很大。綜合表 1、表2數據分析,只要控制熱量損失小、進水冷器的溫度控制得低一些,也有可能達到系統的熱量平衡。
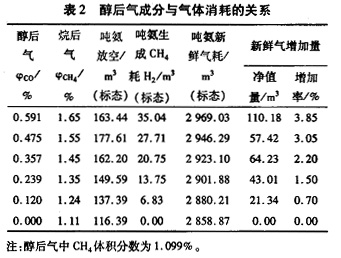
由安淳公司設計并正在使用的雙甲工藝系統中,很多企業(yè)都采用這種帶電爐的操作法,只要控制得法,也達到了安全高效的運行效果。一般每噸總氨的補充熱量均小于10 kW·h(僅幾元錢),也不存在與其它工序相互影響的問題,更不會破壞其它工段的熱平衡。
第1套雙甲工藝在湖南衡陽氮肥廠投產至今已經成功運行了15年,先期為醇烷化工藝,后改成醇烴化工藝,一直采用外供電補熱的方式,實踐證明外供電量消耗醇烴化比醇烷化少得多。通過這一實例,更進一步說明采用醇烴化精制不但可以減少外供熱量、減少原料氣中的H2耗量,同時還可以得到副產品中的醇,創(chuàng)造比烷化精制更好的效益。
3 結語
醇烴化工藝除了具有精制氣體功能外,還利用變換后的CO、脫碳后的CO2副產粗甲醇或醇醚混合物,還可利用醇烴化催化劑生產優(yōu)質的民用燃料,生產中完全可實現零污染和零排放。
該技術發(fā)明之初只有1~2種副產品和單一的流程設置方式,目前已發(fā)展成各種流程配置并能夠生產多種副產品,全國已有近40家企業(yè)采用了這個技術,總氨凈化精制能力40~400 kt/a。無論是雙甲凈化精制工藝還是醇烴化凈化精制工藝,均收到了十分顯著的環(huán)保效益和經濟效益。
安淳公司在設計雙甲工藝流程中,運用了因地制宜的設計方法,不斷優(yōu)化系統,創(chuàng)造了多種工藝的配置和設計模式,在兩級甲醇系統的壓力選擇、各工序壓力級的組合、多種熱利用方式的配備、各工序進出口氣的成分控制及精制方法的選擇上,都進行了深入研究并得到實際應用。
為了將醇烴化工藝推向更節(jié)能、更適用的技術高度,下一步將重點放在與工藝配套的催化劑研究上,使雙甲工藝可以生產醇、醚或烯烴類基礎化工產品,也能夠生產汽油的替代品,以期取得更好的經濟效益和環(huán)保效益。
